Image set
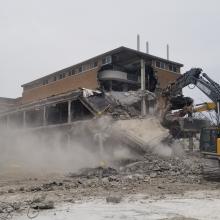
Related services
Related sectors
Related regions
Opening article section
Article section
Lead
Media
Image set
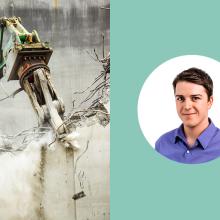
Rich text
The days of the wrecking ball – an iconic symbol of the demolition industry – are over. This inexpensive, easy, and rapid technique avoided weeks of hand-dismantling by work crews, completing the takedown of any building in mere hours and by a single person. Yet today, they are no longer a common sight at structural demolition sites.
The reality is that despite their low cost and efficiency, wrecking balls are a crude, dangerous, and uncontrolled demolition option. Their use sends debris flying, causing structural collapses and smashing through previously-concealed hazardous materials such as asbestos. They also leave behind a pile of pulverized, mixed rubble that must be scooped up and hauled away. These factors have greatly tarnished the wrecking ball’s appeal, especially in densely-packed urban areas.
At the same time, modern builders continue to push the limits of height, size and design for new buildings, and the world of infrastructure, architecture and engineering are rapidly evolving. These unique, modern buildings require creativity and innovation in designing and executing structural demolitions.
Putting safety first
Unlike the wrecking ball, modern demolition is a precise deconstruction process that includes significant safety precautions and a minimal environmental footprint.
In acknowledgement of these facts, provincial governments have gradually introduced stringent new regulations governing demolition. As one example, since 1994 the demolition of one or more buildings in Ontario whose total floor area is at least 2,000 m2 must implement a waste reduction work plan to reduce, reuse, and recycle any waste generated throughout the demolition process, as well as a source separation program to sort through concrete and brick, steel, and wood debris.
Moreover, demolishers must work precisely and carefully, maintaining clean, environmentally-sound sites. Current regulations introduced the implementation of waste reduction work plans to reduce, reuse and recycle waste generated in a demolition project. This includes ensuring the separation of concrete and brick, steel, and wood.
A meticulous, intensive process
A modern demolition project is a meticulous, innovation-driven and multidisciplinary engineering project with structural, environmental, geotechnical, civil, and electrical implications. It frequently starts with a key figure: the demolition engineer.
These professionals classify the sites, identify the unique needs of that site and client, and design a customized demolition strategy to meet the owner’s goals and budget while respecting all applicable regulatory requirements. Once that design is completed, a demolition contractor is retained, and site work begins.
At that point, a host of workers and equipment appear onsite. Crews remove asbestos under appropriate precautions, strip interior wiring, piping, and equipment, remove furniture and windows, and minimize any potential safety and environmental hazards. Utilities are disconnected, adjacent buildings and underground utility tunnels are severed and capped, and heavy equipment arrives for the main event: structural demolition.
Next, the building is systematically deconstructed, and waste materials are sorted and stockpiled. Using heavy-duty hydraulic excavators, exterior finishes are scraped away from the structural elements with precision and stockpiled for disposal. Operators claw, crush, and saw through concrete, steel beams, and rebar, and the building’s foundations are removed.
While operators dismantle the building, other workers are working to maximize profit and safety for people and the environment. Some are crushing waste concrete to recover rebar, loading trucks with steel and copper for recycling, and cleaning copper and aluminum for resale or reuse. Others are hosing down the demolition site to minimize dust, replacing sewer filters, or clearing dust and debris from public roads.
After demolition
Once demolition is complete, a large excavation footprint remains. The next step is environmental remediation of contaminated soils and groundwater where necessary. These soils may be excavated and hauled away for remediation, or treated onsite. Monitoring wells may be installed to monitor and treat any groundwater contaminants.
Once the site's environmental clean-up is finished, the preparation and redevelopment phase begins. Excavations are backfilled with granular material or stone, then compacted, and covered with topsoil and seed. Alternately, excavation may continue for a new development.
Leveraging innovation for safe demolition
So how does a demolition contractor maintain public safety while deconstructing a building in an urban centre, where major roads are bustling with traffic, lane closures are not an option, and operating space is minimal? The key is innovation.
As one example, a 2016 demolition project in a dense downtown core replaced standard construction hoarding with modified shipping container hoarding. Placed end-to-end, these formed a seamless walkway to allow the public to move around safely.
Next, vertical shafts were created to remove concrete from the building’s upper structure and lower it into the basement. Once there, the concrete was spread out within the building’s footprint and crushed into a granular aggregate to backfill the basement cavity.
Using explosives to get the job done
Some larger-scale projects might use explosives for building implosion. This is a highly-specialized, high-risk operation and these projects require a significant amount of prior planning, preparation, and modelling. This option is preferred in rural areas with plenty of surrounding space to ensure public and worker safety.
Selecting the right explosive based on the material to be demolished can contribute heavily to the smooth execution of a structural implosion. The use of dynamite creates a rapid shock of outward pressure that shatters concrete into tiny chunks. For steel structures, RDX is used to generate a concentrated shock that slices through the metal.
Once the explosive has weakened the support structure, gravity does the rest and the building’s own mass will demolish its lower sections. This also pulverizes the lower support structures, making it easier to clean up debris afterward.
Staying competitive
Although their work focuses on environmental concerns and public safety, demolishers must also remain competitive within their industry. By stripping buildings, sorting materials and hauling waste, many demolishers use these high rates of landfill diversion for construction waste (in many cases, above 95%) as a selling point for their business. This factor is becoming increasingly significant when selecting a demolition contractor, given the predominance of environmental concerns in our society today.
Markets and options for construction waste are also growing. Equipment and furniture can be salvaged and refurbished, sold, or donated. Recovered steel, copper, aluminum, and cast iron can be sold at a profit to scrap yards, recycling facilities, and public consumers. Even materials such as brick, concrete, and wood can be resold for small residential projects or used as clean backfill for demolition excavation or other projects.
A feat of modern engineering
Modern demolition is the way of the future in precision deconstruction. Eschewing the historical brute force (and reckless consequences) of the wrecking ball, modern demolition has evolved into an engineering undertaking that is carefully planned, coordinated, and executed. Demolition equipment operations, demolition engineers, and construction labourers alike must be highly-skilled and organized to carry out demolition work that is both safe for the public and environmentally-friendly.