Image set
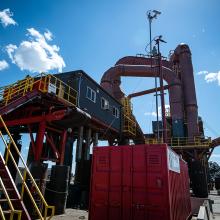
Related services
Related sectors
Related regions
Opening article section
Article section
Rich text
Il y a exactement un an, l’équipe de General Recycling Industries, Ltd. (General Recycling) a célébré une étape importante de son évolution. Après deux ans de consultation, de travaux de conception, de coordination, de planification et de construction, l’équipe était prête à lancer sa nouvelle installation à la fine pointe de la technologie de traitement multi-étapes de la ferraille . Un processus à la base très complexe a pu être simplifié et a permis à l’installation de recyclage de fonctionner avec parfaite fluidité. Capable de traiter plus de 100 tonnes de déchets mélangés par heure, l’installation est tout simplement incroyable. Il s’agit d’un véritable bijou d’ingénierie.
General Recycling a confié à Arrow Engineering, une division d’Englobe (Arrow) l'imposant mandat de conception mécanique, électrique et structurelle, nécessaire à la concrétisation sa vision « déchiqueter pour un avenir meilleur ». Un an plus tard, nous sommes toujours aussi fiers de cette réalisation.
Quand il repense à ce projet, Kevin Mattai, gestionnaire de projet principal, le voit comme l’un des projets les plus passionnants de sa carrière. À l’occasion du premier anniversaire de la mise en service de cette installation de recyclage à grande échelle, nous avons discuté avec lui de l'expertise et du travail accompli en ingénierie à l'origine ce projet unique.
Rich text
Q. En quoi ce projet est-il si spécial ?
R. L’expression peut sembler galvaudée, mais je dirais qu’il s’agit vraiment du type de projet qui n'arrive qu’une fois dans une vie. Sur le plan technologique, c’est l’un des systèmes les plus avancés au Canada : sa capacité de traitement de 80 voitures par heure est impressionnante. Il est composé de deux bâtiments distincts qui fonctionnent en tandem, formant ainsi une installation de recyclage hors du commun. D’un côté, nous avons la déchiqueteuse de voitures, affectueusement appelée « la déchiqueteuse » et de l’autre, le bâtiment où sont acheminés les résidus de ferraille automobile, plus connu sous le nom d’usine ASR (Auto-Scrap Residue). Dans ce système, l’équipement d’exploitation sophistiqué fragmente, trie et récupère les matériaux recyclables des voitures et des appareils ménagers hors d’usage et d’autres déchets métalliques.
Par ailleurs, les impacts environnementaux globaux du projet sont tous aussi remarquables que les opérations elles-mêmes. Modernisée, l’usine de traitement détourne des déchets normalement acheminés dans des sites d’enfouissement, ce qui entraîne une réduction des gaz à effet de serre (GES) de plus de 700 000 tonnes par année, tout en répondant à la demande manufacturière en acier, en aluminium et en cuivre. De plus, le système de déchiquetage et de remise en état est évolutif. Il peut donc adapter sa capacité de traitement proportionnellement à l'augmentation de l’afflux de matières produite par la population croissante. Ainsi, l’usine continuera de préserver les ressources naturelles, d'économiser de l’énergie et de réduire les émissions de GES pendant de nombreuses années.
En plus, General Recycling a acquis une usine de déchiquetage hors service sur la côte ouest pour accueillir sa nouvelle installation de recyclage. Elle sera modernisée et réaménagée pour répondre aux besoins de l’installation.
Media
Image set
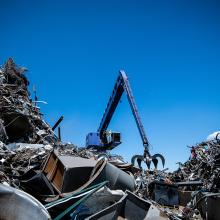
Rich text
Q. Quels ont été les exploits techniques du projet?
R. Une installation de cette ampleur nécessite une quantité d'électricité très importante. C'est pourquoi cela requiert la présence sur site d'une sous-station des services publics pour répondre à cette demande d'énergie. Avant de travailler sur ce projet avec Arrow, le client avait effectué une étude sur la consommation énergétique. Celle-ci indiqua que la nouvelle déchiqueteuse ne serait pas viable en raison de la quantité trop élevée d’électricité nécessaire à son fonctionnement par rapport à la capacité actuelle d’électricité des services publics. Donc, notre équipe a travaillé en étroite collaboration avec les différents intervenants pour trouver une solution. Nous en sommes venus à la conclusion que la déchiqueteuse fonctionnerait adéquatement pendant les heures creuses, c’est-à-dire pendant les heures d’inoccupation des autres immeubles. Un an plus tard, la déchiqueteuse fonctionne à plein régime avec une capacité impressionnante de traitement de 80 voitures par heure. Ce système est réellement impressionnant.
Bien entendu, notre but était d’offrir un meilleur système que l'original. Au lieu d’un moteur de 5 000 chevaux-vapeur, nous avons recommandé deux moteurs de 2 500 chevaux-vapeur, ainsi que des installations intégrées pour l’exploitation et l’entretien, capables de soutenir les opérations quotidiennes du site. Dans le but de s’adapter le mieux possible au climat local et aux conditions du terrain, l’équipe de mécaniciens, au niveau de la conception, a amélioré le chauffage localisé, le refroidissement à grande échelle, la filtration de l’air et la ventilation.
Avec le recul, notre travail collaboratif en tant qu’équipe multidisciplinaire fut une grande réussite. J’ai beaucoup appris en travaillant sur ce projet, notamment sur l’importance de se faire confiance et de ne pas avoir peur des défis.
Media
Image set
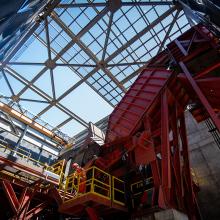
Rich text
Q. Quel est le plus grand défi auquel l’équipe a été confrontée dans le cadre du projet?
R. Je dirais que l’un des plus grands défis a été de concevoir une structure capable d’abriter et de stabiliser l’équipement pour garantir une longue durée de vie à l’installation. La structure du bâtiment de déchiquetage était complexe, car il nous fallait faire bon usage de la gravité pour propulser le matériel de déchiquetage, ce qui impliquait l’installation de deux moteurs de 2 500 chevaux-vapeur au deuxième niveau. La machine à déchiqueter en soi a aussi complexifié le projet. En effet, nous avons dû tenir compte des forces générées par les 12 marteaux en acier de 500 lb qui tournent à 600 tr/min pour les isoler. Pour soutenir le poids important des moteurs et des marteaux, nous avons proposé l’installation d’un mégabloc flottant en béton, qui allait du sol au deuxième niveau et qui a pu ainsi soutenir entièrement le système. Le reste du bâtiment qui héberge la déchiqueteuse a été construit autour du bloc en béton, soutenant toutes les parties de la déchiqueteuse grâce à une fondation solide et distincte, et du fait même, la protégeant des chocs et des forces vibratoires générés par les moteurs.
Par ailleurs, puisqu’il s’agit d’un projet à la fois unique et complexe, sans réel précédent d’un point de vue de l’ingénierie, l’équipe disposait de peu de références sur lesquelles s’appuyer. Mis à part le cabinet d’architecte et l’équipe d’ingénieurs d’Arrow, les partenaires du projet provenaient des quatre coins du monde, des États-Unis à l’Europe. Pour une installation aussi unique en son genre, nous n’avions pas de modèle de conception standard à suivre. Ce type de projet était une première pour notre équipe et nous avons dû concevoir nous-mêmes un ensemble complexe d’équipements spécialisés. Tous les participants ont dû se fier à leur expérience, aux données structurelles et aux particularités de l’équipement pour faire leurs prévisions et concevoir ce projet avec succès. Le travail de conception et d’ingénierie requis dans le cadre de ce projet est tout aussi unique que l’installation elle-même, et c’est un élément dont toute l’équipe peut être fière.
Q. Qu’est-ce qui rend ce projet si mémorable pour vous?
R. Une fois que le système intégré de valorisation multi-étapes a été terminé, quelque chose d’inhabituel s’est produit. Notre client, l’équipe de General Recycling, a invité toute notre équipe d’ingénierie à visiter l’installation. Voir de nos propres yeux le système en action a été une expérience formidable qui a mis en lumière le caractère spécial de ce projet. Nous avons pu observer comment notre travail a permis au client d’avoir un impact environnemental important, ce qui est très gratifiant. Que ce soit la forte augmentation du volume de matériaux détournés des sites d’enfouissement, la quantité de métaux réutilisables remis sur le marché, ou encore l’importante réduction des émissions annuelles de GES, ce projet fait vraiment la différence.
En tant que jeune ingénieur, je pense constamment à l’avenir et espère pouvoir faire une différence et changer le monde. Des projets comme celui-ci me donnent réellement l’impression d’avoir accompli quelque chose d’unique. Je suis extrêmement fier de notre équipe qui a contribué à la conception technique d’une installation vraiment incroyable. Malgré l’absence de modèles de conception au Canada, la tendance est de mettre au point des systèmes durables qui tiennent compte de l’environnement. Ce projet s’inscrit dans cette tendance en démontrant à quel point les ingénieurs peuvent améliorer la vie d’une collectivité.
Kevin Mattai est gestionnaire de projet principal et ingénieur électricien au sein de l’équipe Arrow à Edmonton, en Alberta.